Injection molding MES system
01 Real-time device monitoring, device 0EE analysis
Monitor the real-time status of production line equipment (startup, shutdown, idling, etc.), read the process parameters of equipment, and analyze the utilization rate of equipment.
02 Establish production scheduling and dispatching process control
The system scheduling and dispatching automatically bring out the corresponding mold and machine through the intelligent reminder of the system, and the estimated completion time, so that the work of the production planning personnel is easy and simple, strengthen the process management and control to reduce unnecessary waiting waste.
03 Real-time control of work order production process
Through the system production work order and machine networking binding, real-time tracking of production progress, the system automatic prediction and reminder, reduce the number of production to do more or less, to achieve the purpose of fine management.
04 Automatic statistics of reporting and piecework wages
Through the system to report the work, the system automatically generates the work report statistical report and automatically generates the employee's piecework wage.
05 Process quality management
Paperless entry of the first inspection, inspection and final inspection in the production process, automatic early warning and reminder of key data, statistical analysis of quality data, to achieve the purpose of active management and quality control.
06 Onsite Exception Management
Through the system, all kinds of anomalies in the production process can be timely input and reported by on-site personnel, and various messages can be automatically sent according to the set reporting process to remind managers at all levels, statistical analysis of abnormal situations, and data support for management improvement.
07 The production process can be traced
Through the two-dimensional code of the work order generated by the system, the batch, processing personnel, equipment and other records of the product in the production and processing process are traced.
08 Production mold management
Through the system to achieve the full life cycle management of the mold, mold processing times for automatic statistics, automatically associated with the life of the mold, mold use and maintenance (maintenance times user-defined Settings) for automatic early warning, on-site mold storage location management through the two-dimensional code to achieve rapid mold in and out of the warehouse management.
09 Production equipment management
Through the system to achieve operation and maintenance management, equipment repair, maintenance record management, equipment spot inspection, equipment maintenance management.
10 SOP standard document issued
SOP operation instructions are automatically delivered when I orders are issued by the system, enabling paperless view on site to avoid site management trips and improve site fine management.
11 Visual signage
Through the system to customize a variety of production visual kanban, production schedule kanban, equipment networking kanban, mold life Kanban, lighting kanban, PDCA Kanban and other cockpit kanban.
Data source resolution
Device networking data collection is the most real and timely.
Kanban application scenario
- Workshop task production schedule board
- Device status board
- Injection workshop signage
- Equipment hourly capacity kanban
- PDCA signage
- Die sign
- Quality signage
Workshop task production schedule board
Workshop task production schedule Kanban specific content
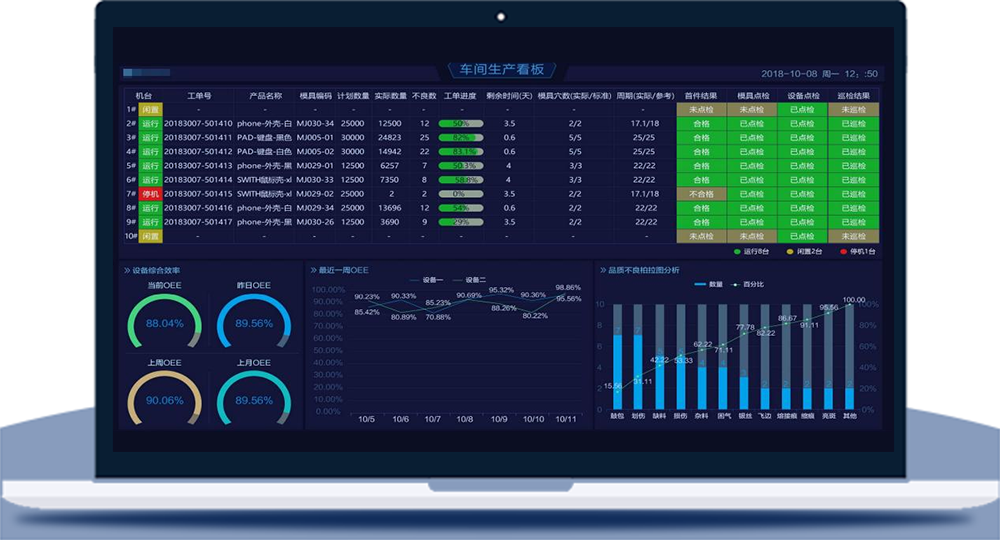
Device status board
Details about the device status Kanban
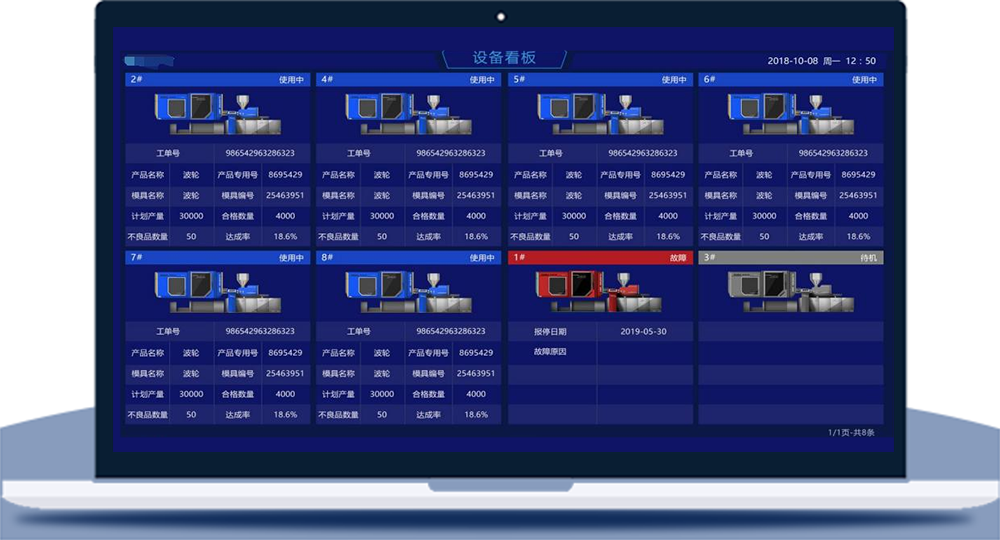
Injection workshop signage
Injection workshop Kanban specific content
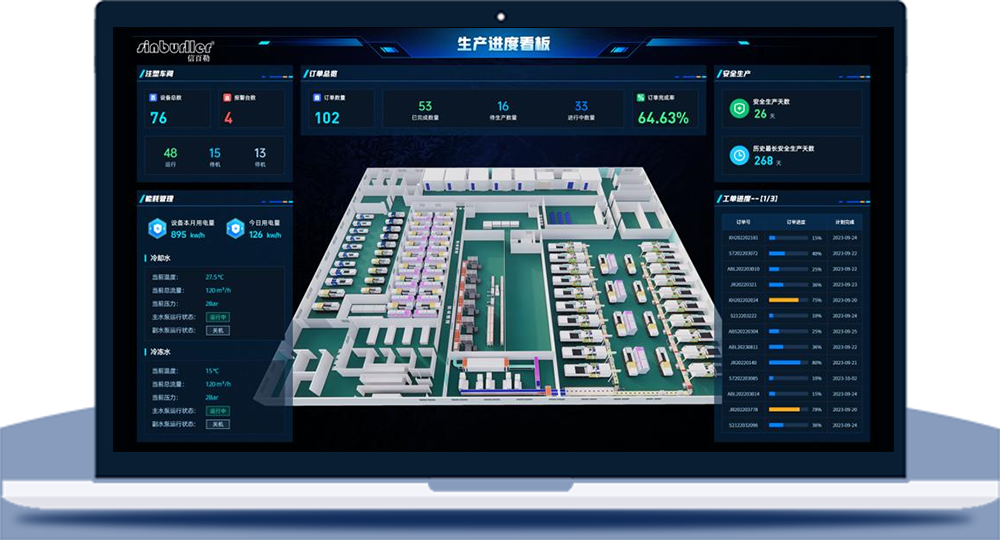
Equipment hourly capacity kanban
Equipment hourly capacity Kanban specific content
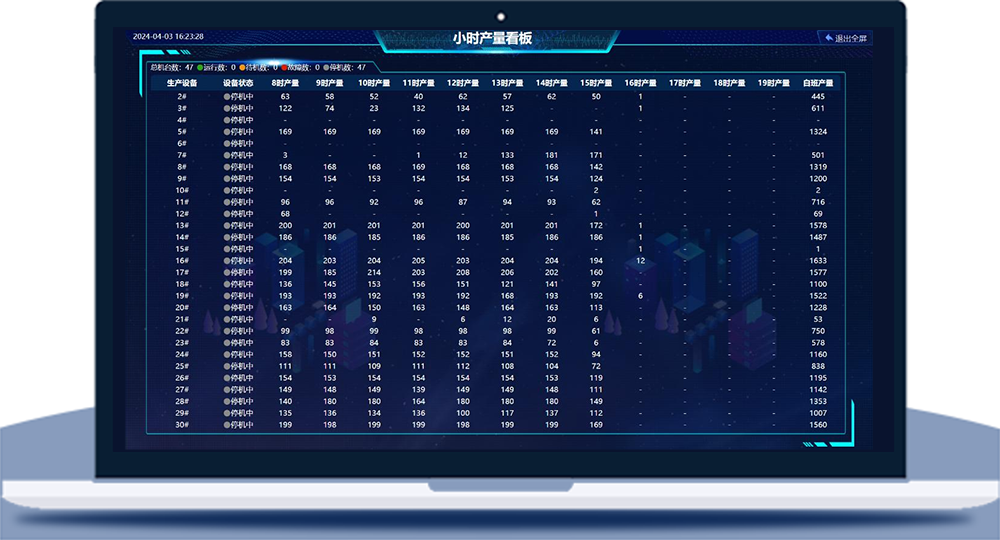
PDCA Kanban Kanban
PDCA Kanban body content
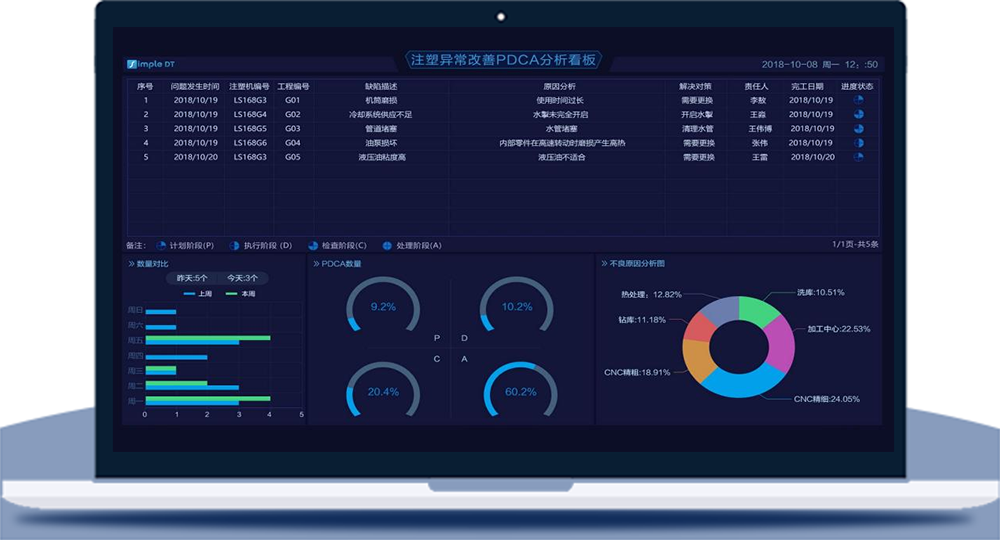
Die sign
Mold kanban specific content
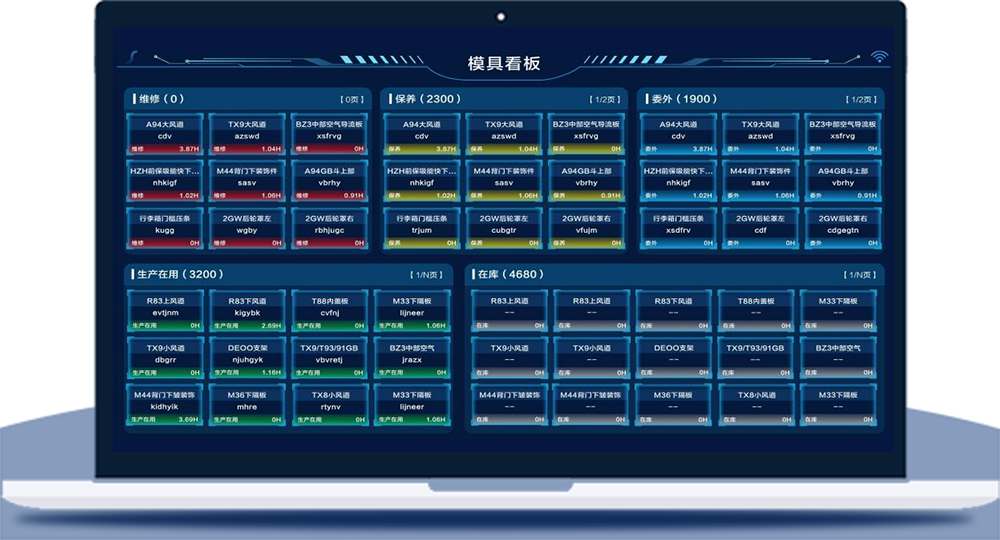
Quality signage
Quality Kanban specific content
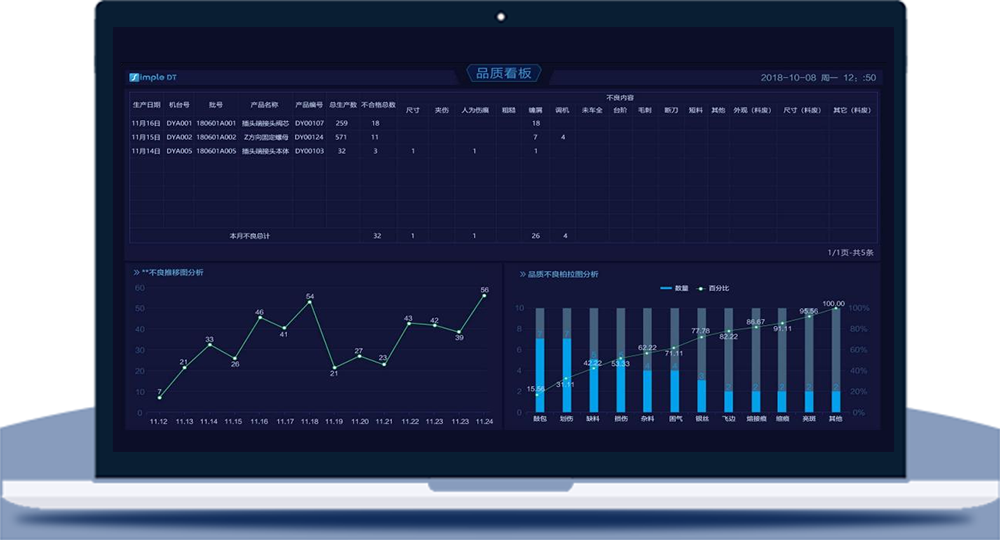